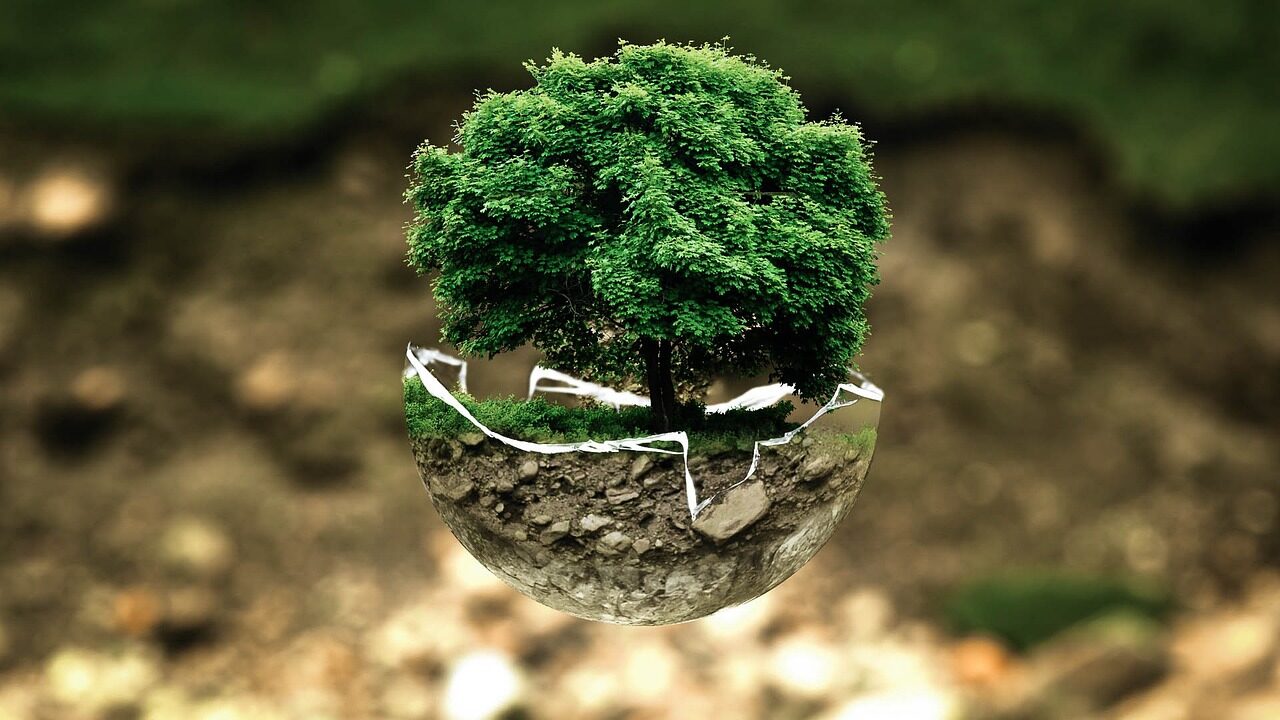
去年,我国提出“3060”双碳目标,“1+N”政策体系逐步落地,在全国,包括北京、上海、广东、深圳等在内已经有 31 个省市陆续制定了双碳目标。绿色成了工业发展的“基本色”,那么,如何在保持业务发展、产能稳定的同时,减少碳排放?这是对很多制造企业提出的“灵魂拷问”。
而谈及“绿色”、“零碳”,不得不提的就是施耐德电气。
作为可持续发展的践行者,施耐德电气将可持续发展融入主营业务的方方面面。施耐德电气长期推进自身的可持续发展转型,将大量绿色的创新产品和数字化技术应用于自身工厂,并取得了不少成果。最直观的是,施耐德电气在全球打造了 64 家“零碳工厂”,在中国 23 家工厂中,就有 15 家已经实现“零碳”。
坐落于北京亦庄的施耐德(北京)中低压电器有限公司(以下简称“北京工厂”),就是这 15 个“零碳工厂”之一,除此之外,它还是工信部认证的国家级“绿色工厂”,以及施耐德电气全球“智慧工厂”项目中的样板工厂。去年,北京工厂还经过了中国船级社质量认证公司的碳中和认证并获颁“碳中和”证书,成为全国首家“碳中和”工厂,是施耐德电气“绿色”发展之路上的又一里程碑。
在日前的施耐德电气“创新开放日”之际,InfoQ 等媒体一起探访了北京亦庄工厂,看这座“零碳工厂”如何在持续增长的同时,实现节能减排的目标。
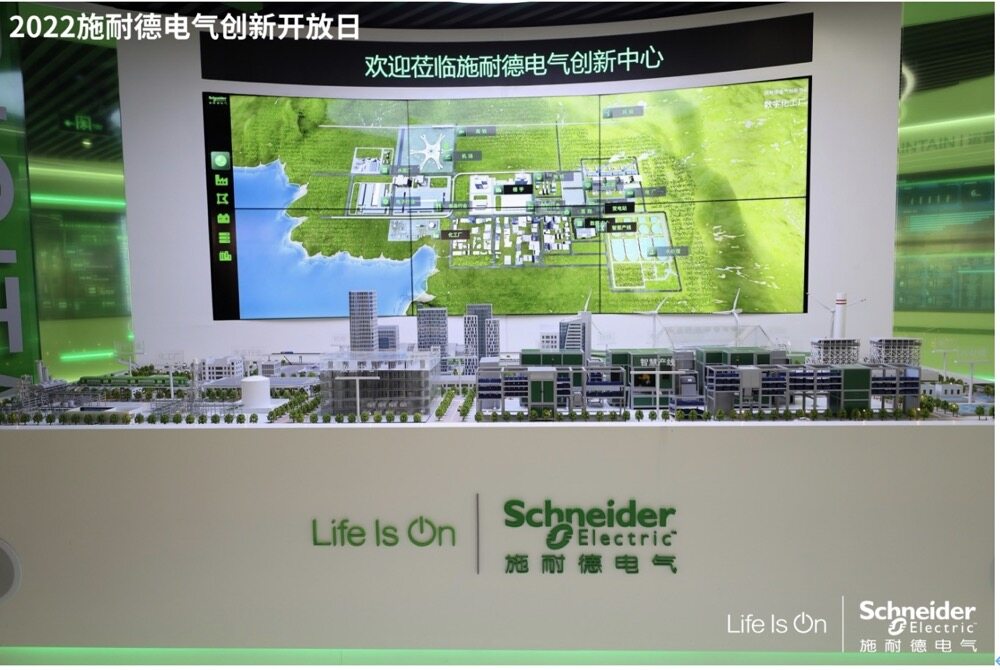
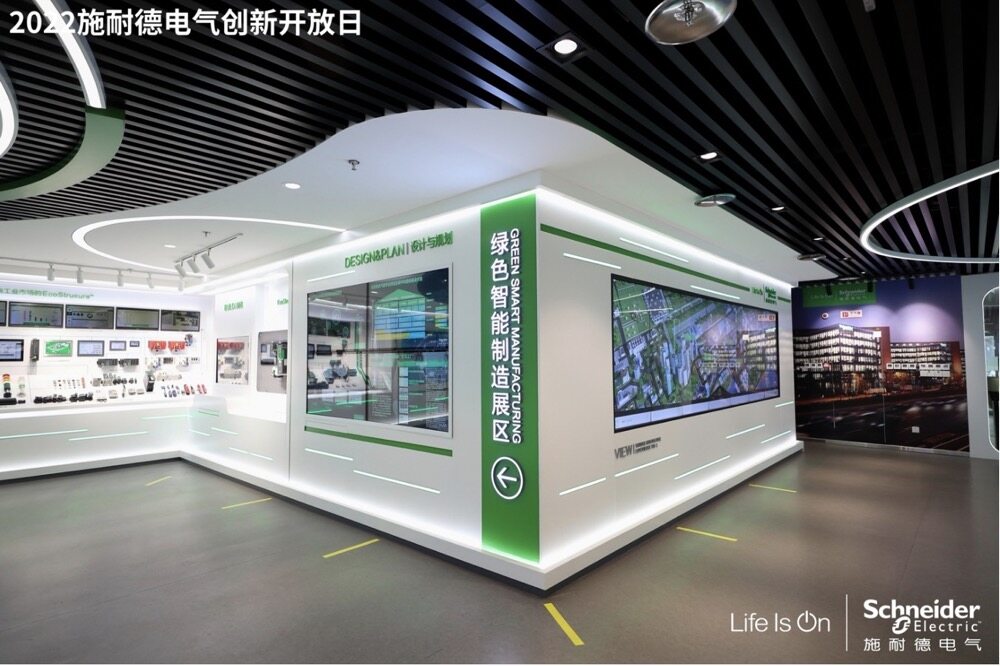
提升能源效率,既靠技术也靠绩效
根据国际能源署(IEA)发布的《全球能源评估:2021 年二氧化碳排放》报告显示,2021 年,全球温室气体排放量达到了 408 亿吨二氧化碳当量,能源相关的二氧化碳排放量达到了 363 亿吨,占比超过 88%。
这意味着,能源将是企业实现绿色生产的关键突破口。
在北京工厂,施耐德电气主要从三方面着手:第一,部署清洁能源,增加可再生能源的使用;第二,搭建数字化能源监控系统,提升能源使用效率,避免浪费;第三,通过智能调度,优化产线的能源管理,实现能源价值最大化。
比如,从源头上,北京工厂部署了施耐德电气在中国最大的光伏项目基地,,增加了清洁能源的使用比重——具体占全厂能源使用的 30%,据统计,这样下来每年可以减少超过 2000 吨的碳排放。但是,碳排放存在于生产的全过程中,更繁重的减排任务主要是对另外 70%的传统能源的效率优化上。
在施耐德电气看来,数字化技术是能效优化的基础,通过广泛采集生产线上的水、电、气等与能源相关的数据,借助大数据的监测和分析手段,可以实现对各项能耗指标的可视化管理,根据能耗高峰和低谷进行调优,避免资源浪费。
以空调冷机为例,基于冷库预测模型和冷机测试模型,可以预测未来 24 小时的天气数据、人流数据、室内温度数据等等,根据这些数据,工厂就可以对冷机的开关机策略进行优化,决定在什么时间段开启和关闭,避免在非必要的情况下长时间启动,造成资源浪费。
据了解,北京工厂内已经安装了数以万计的传感器,基于全套数字化监控系统,可以对生产全过程产生的各项能耗指标进行持续改善,把各个环节的碳排放降到最低。
除此之外,在数据基础上,施耐德电气北京亦庄工厂还通过与第三方服务的打通,实现智能调度,降低对传统能源的依赖。比如,根据市电实时电价等变量,优化能源使用结构,在用电高峰使用新能源,在用电低谷再切换成传统用电,这一方面节省了用电成本,同时也降低了碳排放。
不过,数字化技术固然可以在这一系列节能减排举措中帮助企业解决大量复杂问题,但措施能否顺利落地,关键还在于“人”——即人在其中的决心和驱动力。为此,施耐德电气还为工厂中的不同部门和角色设定了能源绩效 KPI,让节能减排这件事与每个人变得息息相关。
值得强调的是,这里的能源绩效的设定办法,同样是基于现场能源、能耗数据的积累和测算,而不是拍脑门的“一刀切”,根据不同车间、不同产线和不同班组的具体情况,会有差异化的管理指标。
生产效率优化,反向减少能源消耗
施耐德电气非常看重软件在绿色生产过程中发挥的价值。在其看来,碳管理是一个系统性工程,必须建立全生命周期的碳管理,其中,软件技术相当于一个“中枢”,可以实时收集、分析、呈现“碳足迹”,在发掘减碳机会的同时,提升生产的效率和能效,达到“控碳”的目的。
拿北京工厂来说,这个国家级“绿色工厂”的底层,基于的是施耐德电气在 2017 年全新升级的 EcoStruxure 架构与平台,工厂的生产、运营流程和能效等方面的数据都会被整合到这一平台上统一管理。
比如对于光伏这样的新能源来说,虽然清洁,但是容易受天气等因素的影响,存在一定的波动性。所以,想要加大新能源使用,前提必须是稳定用电、保障生产,这需要更精细化的管理。拿前文介绍的智能调度场景为例,其背后应用的是施耐德电气的 EcoStruxure 微网能源顾问平台。
该平台基于 AI 技术,通过运行模型预测控制算法来定义微电网的优化策略。具体来说,算法结合了电价信号、历史数据、天气数据和运行时间表等信息,可以预测工厂微电网边界内的能源供需变化,据此协调光伏发电量与储能系统运作,从而消除电力峰谷差,实时优化能源调度。正是借助这些软件的赋能,施耐德电气才得以从设计、建造到运维,使得全生命周期减碳成为可能。
而相比实现能源消耗的全流程可视化管理这种直接了当的手段,工厂的节能减排还有另一个思路,即通过提升工厂的生产效率,反向减少能源消耗。
以宝钢为例,借助借助施耐德电气的EcoStruxure平台,宝钢对工厂进行了升级改造,最终实现了 30%的产量提升。比如,在仓库板坯搬运的场景,通过部署无人起重系统,板坯库倒垛率由原来的 30%提升至现在的 70%~80%左右,平均日产量达到了 10,500 吨。
这一方面减少了人工成本产生的碳足迹,另一方面,在效率提升之后,仓库的光、电等能源也会得到节约。换句话说,工厂的绿色发展,并不一定要牺牲生产本身,在确保生产有序进行的同时,还可以通过正向的效率提升,反过来推动低碳目标的实现。
自动化是实现全生命周期碳管理的前提
施耐德电气副总裁、数字化服务业务中国区负责人张磊表示,随着相关政策的陆续落地,碳管理的工作越来越细化到每个行业和每个企业,呈现出差异化的趋势。目前,施耐德电气主要服务于包括工业、楼宇、数据中心、基础设施、家居等市场。
以建筑行业为例,通常建筑行业最大的能耗设备就是空调,这意味着,空调的运行数据是楼宇需要重点管理的对象。而工业生产线可能要更复杂,大量的生产装备、降温设备、冷机设备等等,需要更体系化、精细化的能源规划。从企业内部来说,这意味着除了生产过程,还要在研发、库存、运输、回收等各个环节,也融入低碳思想,并部署相关技术来衡量、执行和管理减碳过程;从外部来说,这还涉及供应链和生态伙伴的管理和配合。
但是,由于自动化水平的差异,IT 与 OT 发展割裂,目前很多企业没办法在生产的过程中采集到能耗相关的数据,或者不同条线采集到的数据不一致且无法打通,导致无法合理地指导能源管理的优化。所以,在施耐德电气看来,自动化和数字化是对碳足迹进行充分追踪和管理的前提。
张磊表示,企业要让软件的价值最大化,其关键是以 IT 与 OT 的融合,为软件发挥作用搭建基石。一直以来,施耐德电气都致力于以 IT 与 OT 深度融合,结合从规划到落地的咨询服务,助力产业全程减碳。为实现这一目标,施耐德电气中国软件研发中心自去年成立以来,已经对其物联网平台实现了更新升级,其中提供了 18 项算法服务,实现了 99.9%的云服务率,并汇聚了 18 家技术合作伙伴。
而技术的应用,也需要符合企业的长期双碳规划方可发挥效用。“在帮助企业实现双碳目标的过程中,施耐德电气一方面会帮助企业用好技术,另一方面也会先通过咨询形式,为企业诊断在能源管理、运营管理中存在的问题,然后再针对问题,确定具体的解决方式——比如只是需要简单改造、上线一些应用软件,还是需要改变整个组织形式——我们认为,这个过程是需要‘先医后药’的。”张磊告诉记者。
据了解,2021 年施耐德电气推出了五大碳中和服务成果,为企业提供数字化治碳从规划到落地的完整服务。并且,在工业领域,还通过整合智能工厂规划咨询、智能工厂相关的软件系统、底层元器件和设备等能力,形成了绿色智能制造解决方案推动工业企业全生命周期效率的提升。
“我们发现,对于国内很多制造企业来说,OT 是更加迫切的需求。所以,眼下我们最重要的任务就是先帮助他们实现自动化控制,先把数据的真实性问题解决掉,解决好基本管理的需求,再进一步推动后续的数字化转型。”针对转型的现实路径,张磊总结到。在这个过程中,施耐德电气自身既是实践者也是赋能者,作为能源管理和自动化两个领域的“斜杠”专家,其绿色理念也将经由技术和服务输出,推向其它行业。
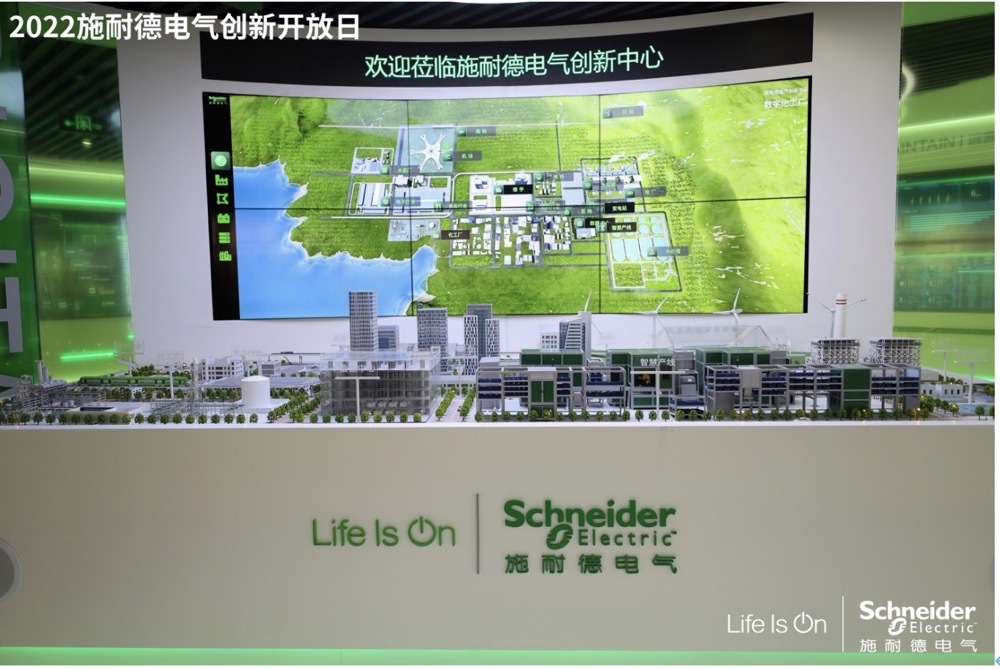
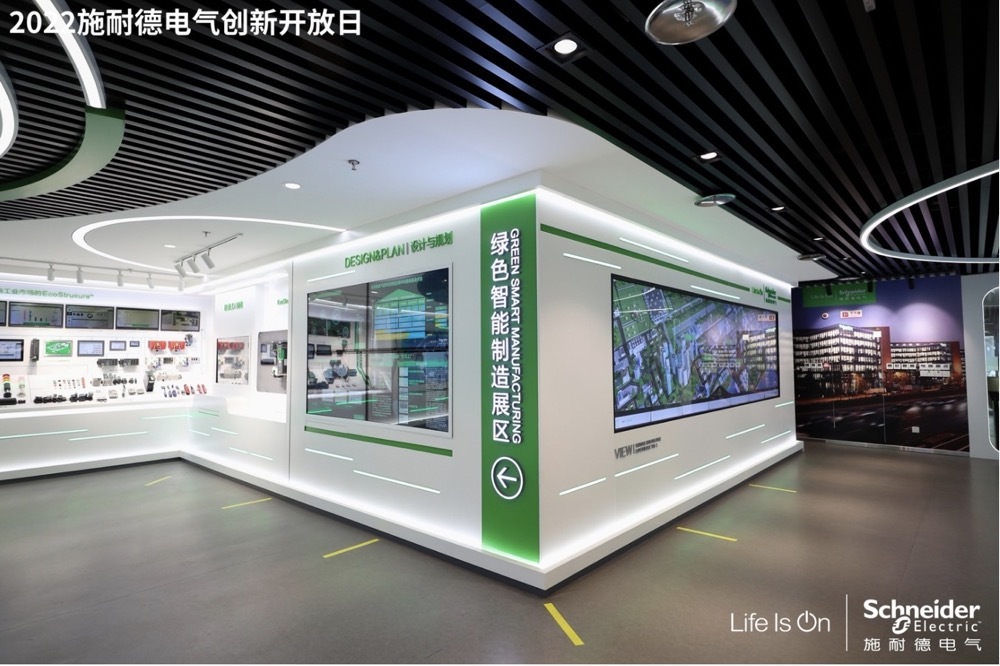
评论